|
|
|
|
|
|
|
|
|
|
|
|
|
|
|
|
|
|
|
|
|
|
|
|
|
|
|
|
|
|
|
|
|
|
|
|
|
|
|
|
|
|
|
|
|
|
|
|
|
|
|
|
|
|
|
|
|
|
|
|
|
|
|
|
|
|
|
|
|
|
|
|
|
|
|
|
|
|
|
|
|
|
|
|
|
|
|
|
|
|
|
|
|
|
|
|
|
|
|
Brake system
Servo-assisted brakes are fitted. This system consists of a normal hydraulic system with the addition of a slave master cylinder, operated by a vacuum servo unit connected to the induction system via a non-return valve.
As the power for this braking system is derived from the engine itself, it is inadvisable to coast downhill with the engine stopped.
Should the servo unit fail the brakes will continue to function through the normal hydraulic system when the brake pedal is depressed, but more foot pressure will be required than formerly.
Under exceptionally heavy duty conditions where the brakes are being used to their maximum continuously the brake fluid must be completely pumped out and replaced with new fluid whenever the front brake pads are renewed.
Brake fluid reservoir
The fluid reservoir for the hydraulic brake system, which should be checked every 3,000 miles (5.000 km), is mounted on the wing valance on the same side as the brake pedal.
The brake fluid reservoir cap incorporates a float level and a switch, which operates the rectangular amber warning light on the instrument panel, should the level in the reservoir fall below the safe limit.
When removing reservoir cap do not disconnect the wires; however, care should be taken when withdrawing the float unit to ensure that the brake fluid does not drip on to the car, The correct level is with the reservoir filled to the rib on the filter. The rectangular amber warning light operates in two ways as follows:
1. It is also used to indicate that the level of the brake fluid in the reservoir has dropped below the safe limit. Should therefore, the light come on at any time when the handbrake is off, immediately investigate the cause, in this event the level in the brake reservoir tank must in any case be checked and replenished if necessary.
2. It also gives, when the ignition is on, visual indication that the handbrake is applied. Before starting to drive off, ensure that
the light is extinguished by releasing the handbrake.
Check operation of reservoir level safety switch every 3,000 miles (5.000 km) as follows:
Ignition 'on', handbrake 'off', unscrew and lift filler cap, when the warning light should be illuminated.
The correct fluid level is with the reservoir filled to the rib of the filter; occasionally, remove the filler cap and replenish as necessary, using only Girling Crimson Brake Fluid (obtainable from any Rover distributor or dealer).
It is advisable to check this point regularly, as shortage of fluid will result in gradual deterioration of the brakes which may not be noticed by the driver.
|
|
|
|
|
|
|
|
|
|
|

Brake fluid reservoir |
|
|
|
|
|
|
|

Rear wheel brake adjustment |
|
|
|
|
|
|
|
|
|
|
|
|
|
|
|
|
|
|
|
|
|
|
|
|
|
|
|
|
|
|
|
|
|
|
|
|
|
|
|
|
|
|
|
|
|
|
|
|
|
|
|
|
|
|
|
|
|
|
|
|
|
|
|
|
|
|
|
|
|
|
|
|
|
|
|
|
|
|
Foot brake adjustment
When brake lining wear has reached a point where the pedal travel becomes excessive, it is necessary to adjust the shoes in closer relation to the rear brake drums.
Proceed as follows:
Front
Hydraulic disc brakes are fitted on the front, and the correct brake adjustment is automatically maintained; no provision is therefore made for adjustment. Check minimum thickness of pads, which should not be less than 0.125 in, (3 mm).
Rear
Check, and if necessary adjust the brake shoes every 3,000 miles (5.000 km). They are adjusted by means of a single adjuster assembly fitted at the forward side of the brake anchor plate which allows the shoes to expand or contract equally.
1. With the rear wheels jacked up, ensure that they rotate freely; slacken the adjuster if necessary, by turning anti-clockwise.
2. Apply the foot brake to ensure that the shoes are bedded in and turn the adjuster clockwise until the linings brush the brake drum, then slacken adjuster off two clicks.
Hand brake adjustment
If movement on the lever should become excessive, it may be reduced by means of the adjustment on the operating rod, accessible when the cover is removed.
-Adjust rear brakes as above, then linkage should be set so that the lever has one or two "clicks" free movement in the "off" position.
|
|
|
|
|
|
|
|
|

Hand brake adjustment
A-Adjusting nut
B-Locknut |
|
|
|
|
|
|
|
|
|

Brake bleed nipple
|
|
|
|
|
|
|
|
|
|
|
|
|
|
|
|
|
|
|
|
|
|
|
|
|
|
|
|
|
|
|
|
|
|
|
|
|
|
|
|
|
|
|
|
|
|
|
|
|
|
|
|
|
|
|
|
|
|
|
|
|
|
|
|
|
|
|
|
|
|
|
|
|
|
|
|
Bleeding the brake system
If the level of fluid in the reservoir is allowed to fall too low, or if any section of the brake pipe system is disconnected, the brakes will feel "spongy", due to air having been absorbed into the system. This air lock must be removed by bleeding the hydraulic system at the wheel cylinders; bleeding must always be carried out at all wheels, irrespective of which portion of the pipe-line is affected:
1. Slacken the shoe adjusters right off. Rear brakes only.
2. Attach a length of rubber tubing to the bleed nipple on the wheel unit farthest from the brake pedal and place the lower end of the tube in a glass jar.
3. Slacken the bleed screw and pump the brake pedal sharply two or three times and then more slowly, pausing at each end of each stroke, until the fluid issuing from the tube shows no signs of air bubbles when the tube is held below the surface of the fluid in the jar.
4. Hold the tube under the fluid surface and with the foot]brake fully depressed, tighten the bleed screw.
5. Repeat for the other three wheels in turn, finishing at the one nearest the brake pedal.
6. Re-adjust the rear brakes.
The fluid in the reservoir should be replenished throughout theoperation with new fluid to prevent another air lock beinig formed.
Air filter for servo
The air filter element on the servo unit should be renewed every 12,000 miles (20.000 km) as follows:
1. Spring off retainer, remove plastic cover and filter element.
2. Fit new filter element, replace plastic cover and spring retainer into position.
|
|
|
|
|
|
|

Air filter for brake servo unit |
|
|
|
|
|
|
|
|
|

Clutch Adjustment |
|
|
|
|
|
|
|
|
|
|
|
|
|
|
|
|
|
|
|
|
|
|
|
|
|
|
|
|
|
|
|
|
|
|
|
|
|
|
|
|
|
|
|
|
|
|
|
|
|
|
|
|
|
|
|
|
|
|
|
|
|
|
|
|
|
|
|
|
|
|
|
|
|
|
|
|
|
|
|
|
Clutch
The clutch must only be used when starting the car from rest or when changing gear; at all other times the foot should. be kept clear of the clutch pedal, to avoid unnecessary lining wear.
Clutch adjustment
To ensure efficient operation of the clutch unit, there must be free movement in the linkage, to the extent of 0.75 in. (20 mm) meatured at the pedal pad.
Check, and if necessary adjust the clutch free pedal movement every 6,000 miles (10.000 km), as follows:
Slacken the locknut, rotate the adjusting nut which is machined so that it locks itself at every half-turn, until free move ment at pedal pad is correct.
Re-tighten locknut.
The clutch spring anchor mounted on the bell housing has three spaced securing holes, so that the spring tension may be adjusted to suit individual drivers.
Fuel pump A dual fuel pump is fitted in the luggage boot at the right-hand side and is protected by a detachable cover.
The main pump will operate immediately the ignition is switched on, so filling the carburetter float chamber and ensuring easy starting.
The reserve pump is operated by the left centre switch on the instrument panel and draws on approximately 1 to 1.5 gallons
(4 to 7 litres) reserve fuel.
Fuel sediment bowl
The sediment bowl, mounted on the wing valance, provides an additional filter between pump and carburetter, and should be cleaned every 12,000 miles (20.000 km) or more frequently if an appreciable amount of foreign matter can be seen in the bowl.
Proceed as follows:
(a) Remove the bowl by slackening the thumb screw and swinging the retainer aside.
(b) Remove and clean filter gauze in petrol.
(c) Ensure that the sealing washer is in good condition.
(d) Replace gauze and refit bowl.
|
|
|
|
|
|
|
|
|

Dual fuel pump |
|
|
|
|
|
|
|
|
|

Fuel sediment bowl
|
|
|
|
|
|
|
|
|
|
|
|
|
|
|
|
|
|
|
|
|
|
|
|
|
|
|
|
|
|
|
|
|
|
|
|
|
|
|
|
|
|
|
|
|
|
|
|
|
|
|
Tyre pressures
Maximum tyre life and performance will be obtained only if the tyres are maintained at the correct pressures.
Rover 95 only: Normal motoring |
|
|
|
|
|
|
|
|
|
Front
Normal Load
|
Font
Fully Laden
|
Rear
Normal Load
|
Rear
Fully laden
|
|
lb/sq.in
|
28
|
30
|
24
|
30
|
|
kg/cm^2
|
1,9
|
2,1
|
1,7
|
2,1
|
|
|
|
|
|
|
|
|
|
|
|
|
|
|
|
|
|
|
|
|
|
|
|
|
|
|
|
|
|
|
|
|
|
|
|
|
|
|
|
|
|
|
|
|
|
|
|
|
|
|
|
|
|
|
|
|
Rover 95 only. For sustained high speed motoring, that is speeds in excess of 80 m.p.h. (120 k.p.h.) for more than a few minutes, it is essential from the viewpoint of safety and satisfactory tyre life to increase tyre pressures as shown below:
Rover 95 only: High speed motoring Increase tyre pressures by 6 lb/sq.in. (0,4 kg/cm^2).
Road speed tyres are fitted as standard equipment to all 110 models and the following pressures should be maintained:
|
|
|
|
|
|
|
|
|
|
Rover 110 only:
|
|
All loads and speeds up to 100 m.p.h. (160 k.p.h,)
|
Speeds over 100 m.p.h. (160 k.p.h.)
|
|
Front
|
Rear
|
Front
|
Rear
|
|
28 lb/sq.in
1,9 kg/cm^2
|
26 lb/sq.in.
1,8 kg/cm^2
|
32 lb/sq.in.
2,2 kg/cm^2
|
30 lb/sq.in.
2,1 kg/cm^2
|
|
|
|
|
|
|
|
|
|
|
|
|
|
|
|
|
|
|
|
|
|
|
|
|
|
|
|
|
|
|
|
|
|
|
|
|
|
|
|
|
|
|
|
|
|
|
|
|
|
|
|
|
|
Pressures should be checked and adjusted weekly and at every maintenance attention, paying attention to the following points. When high speed touring, it is very important that the tyre pressures are increased as detailed and checked much more frequently, even to the extent of a daily check.
At high speeds tyres become hot and pressure increases; do not reduce pressure if tyres are checked under these conditions.
Whenever possible check with the tyres cold, as the pressure is about 3 lb. (0,2 kg) higher at running temperature.
Always replace the valve caps, as they form a positive seal on the valves.
Any unusual pressure loss in excess of 1 lb. (0,05 kg) per week, should be investigated and corrected.
Always check the spare wheel, so that it is ready for use at any time.
At the same time, remove embedded flints, etc., from the tyre treads with the aid of a penknife or similar tool. Clean off any oil or grease on the tyres, using petrol sparingly.
Changing wheel positions
It is recommended that the wheels are changed round every 3,000 miles (5.000 km) as illus 4 trated, to equalise tyre wear,
Wheel and tyre balance
Wheel and tyre units are accurately balanced on initial assembly with the aid of clip-on weights secured to the wheel rim.
In order to obtain the important feature of dynamic balance it is advisable that wheel balance should be checked every 6,000 miles (10.000 km); it must always be done when new tyres are fitted.
Road springs, rear
Every 12,000 miles (20.000 km) check the security of the nuts of the U-bolts securing the axle to the springs; tighten as necessary.
|
|
|
|
|
|
|
|
|
|
|
|
|

Changing wheel positions |
|
|
|

U-bolts and rear spring mounting |
|
|
|
|
|
|
|
|
|
|
|
|
|
|
|
|
|
|
|
|
|
|
|
|
|
|
|
|
|
|
|
|
|
|
|
|
|
|
|
|
|
|
|
|
|
|
|
|
Propeller shaft lubrication
Every 6,000 miles (10.000 km) apply one of the recommended greases at the lubrication nipple on the sliding portion of rear propeller shaft.
Fully sealed journals are fitted, and these require no lubrication.
Battery
The positive earth 12 volt battery is carried under the rear seat on the right-hand side and is accessible, after withdrawing the seat cushion, by removing the cover plate exposed.
Every 3,000 miles (5.000 km) check the battery level as follows:
1. Remove cover by releasing the screws and securing clips.
2. Wipe all dirt and moisture torn the battery top.
3. Remove the filler plug from each cell in turn. If necessary add sufficient distilled water to raise the level to the top of separators. Replace the filler plug. Avoid the use of a naked light when examining the cells.
4. Replace cover and retain by means of the clips and screws. |
|
|
|
|
|
|
|
|

Propeller Shaft Lubrication |
|
|
|
|
|
|
|
|
|
|
|
|
|
|
|
|
|
|
|
|
|
|
|
|
|
|
|
|
|
|
|
|
|
|
|

Battery |
|
|
|
|
|
|
|
|
|
|
|
|
|
|
|
|
|
|
|
|
|
|
|
|
|
|
|
|
|
|
|
|
|
|
|
|
|
|
|
|
|
|
|
|
|
|
|
|
|
In hot climates it will be necessary to top-up the battery at more frequent intervals.
In very cold weather it is essential that the vehicle be used immediately after topping-up, to ensure that the distilled water is thoroughly mixed with the electrolyte. Neglect of this precaution may result in the distilled water freezing and causing damage to the battery.
Every 6,000 miles (10.000 km) clean, grease and tighten battery terminals.
Current-voltage control box
The current-voltage control, fuse and junction boxes are housed on the engine side of the scuttle, all but the control box being covered by a plate bearing an explanation of the connections; this plate is retained by two thumb screws and shakeproof washers.
The cut-out and regulator in the control box are set on initial assembly and must not be tampered with; the protecting cover is
therefore sealed.
Fuse box
The fuse termed A2' protects the accessories which are connected so that they operate irrespective of whether the ignition is on or off.
These are clock, map light and A-Fuse, 35 amp. interior lights.
The fuse termed 'A4' protects the accessories which are connected so that they operate only when the ignition is switched
on. These are windscreen wipers, heater, direction indicators, stop lights, petrol level gauge, petrol reserve switch and reverse light. The instrument panel lights are protected by a fuse unit clipped to the harness below the main fuse box.
All other components are not fused.
On 110 models, the fuse for the overdrive unit is situated to the right on the engine side of the scuttle.
A blown overdrive unit fuse is indicated as follows:
(a) When in top gear, unable to engage overdrive.
(b) When in overdrive, the unit will re-engage normal drive irrespective of throttle opening.
35 amp. cartridge type fuses must be used for all replacements. |
|
|
|
|
|
|
|
|
|
|
|
|
|
|
|
|
|
|
|
|
|
|
|
|
|
|
|
|
|
|
|
|
|
|
|
|
|
|
|
|
|
|
|
|
|
|
|
|
|
|
|
|

Fuse box |
|
|
|
|
|
|
|
|
|
|
|
|
|
|
|
|
|
|
|
|
|
|
|
|
|
|
|
|
|
|
|
|
|
|

Headlamp |
|
|
|
|
|
|
|
|
|
|
|
|
|
|
|
|
|
|
|
|
|
|
|
|
|
|
|
|
|
|
|
|
|
|
|
|
|
|
|
|
|
|
|
|
|
|
|
Headlamps
The headlamps are mounted in the wings; to replace a unit or a bulb slacken the screw at the bottom of the headlamp rim and lift off the rim. Replacement bulb type: Remove dust-excluding rubber. Press in the light unit against the tension of the springs on the three adjustment screws, turn it anti-clockwise and withdraw. Twist the adaptor in an anti-clockwise direction and pull it off the light unit; the bulb can then be replaced and the unit reassembled.
Sealed beam type: Remove the retaining rim maintained in position by three recessed head screws. Withdraw the headlamp unit and disconnect the plug at the rear. Replace the unit and reassemble.
Replacement bulbs:
Headlamps (R.H.D. models): Lucas Sealed Beam, 12 v., 42/36
Headlamps (L.H.D. models except North America and Europe): Lucas No. 355, 12 v., 42/36 double filament (dip to right).
Headlamps (Europe except France): Lucas No. 410, 12 v., 45/40 double filament (duplo) (vertical dip).
Headlamps (France): Lucas No. 411, 12 v., 45/40 (duplo, yellow).
Headlamps (North America): Special 12 v.
Headlamp setting
Check the headlamps every 6,000 miles (10.000 km). They should be set so that the main driving beams are parallel with the road surface. If adjustment is required, remove the rim as described above. The vertical setting can then be made by turning the screw at the top of the lamp and horizontal adjustment by means of the screw at the side of the unit.
In order to adjust headlamps, using a beam proceed as follows:
1. Mark on the board the dimensions shown position the car, unladen, on level ground. setting board, in sketch and
2. Place the board 12 ft. (365 cm) in front of the headlamps, ensuring that it is at right angles to the car centre line and that the centre line on the board is in the same plane-as the car centre line.
3. Adjust the beam by turning the adjusting screws until the area of concentrated light corresponds with the marks on the beam setting board,
Side lamps
The side lamps are mounted in the front wings. Prise up rubber lip and remove chrome rim complete with glass. The bulb can then be replaced and the unit reassembled.
Replacement bulbs- Lucas No. 207, 12 v., 6 w.
|
|
|
|
Headlamp setting board dimensions
A-35.5 in. (890 mm)
B-concentrated area of light L.H. headlamp
C - concentrated area of light R.H. headlamp
D -30.56, in. (840 mm)
E -Ground level |
|
|
|
|
|
|
|
|
|
|
|
|
|
|
|
|
|
|
|
|
|
|
 |
|
|
|
|

Side Lamp
|
|
|
|
|
|
|
|
|
|
|
|
|
|
|
|
|
|
|
|
|
|
|
|
|
|
|
|
|
|
|
|
|
|
|
|
|
|
|
|
|
|
|
|
|
|
|
|
|
|
|
|
|
|
|
|
|
|
|
|
|
|
|
|
|
|
|
|
|
|
|
|
|
|
|
|
|
|
|
|
|
|
|
|
|
|
|
|
|
Rear lamps
The rear lamps combine tail light, stop light, direction indication light and reflector.
To replace bulbs: slacken the two securing screws and remove the rim assembly. The lower (dual filament) bulb is the stop tail bulb while the second bulb, fitted in the upper socket, acts as a direction indicator.
Replacement bulbs:
Stop-tail lamp: Lucas No. 380, 12 v., 21/6 w.
Indicator lamp:
Lucas No, 382, 12 v., 21 w.
Direction indicator lamps
Flashing type indicators with amber lens are fitted as standard equipment.
The forward facing lamps are located in the front wing above the side lamps, while at the rear flasher bulbs are contained in the rear lamps. A special unit in the circuit causes either the left-hand or right-hand lamps to flash when the steering column control is operated.
To change a bulb proceed as follows:
Front indicator lamps
Turn the lamp glass and rim in an anti-clockwise direction until it can be lifted off; renew the bulb, press on the glass and rim and turn clockwise as far as possible.
Rear indicator lamps
Proceed as for rear lamp above.
Replacement bulbs:
Front indicator lamp: Lucas No. 382, 12 v., 21 w.
Rear indicator lamp: Lucas No. 382, 12 v., 21 w.
Rear number plate illumination and reversing lamp
The rear number plate illumination lamp is mounted on the boot lid above the number plate.
The two outer bulbs illuminate the number plate when the main lamp switch is on; the centre bulb, operated automatically
by the reverse gear mechanism, provides a rearward light when reversing.
To replace a bulb: Remove two retaining screws and lift off top cover, and replace bulb as required.
Replacement bulbs:
Number plate illumination lamp: Lucas No. 222, 12 v., 4 w.
Reversing lamp: Lucas No. 382, 12 v., 21 w.
|
|
|
|
|
|

Rear Lamp |
|
|
|
|

Front indicator lamp |
|
|
|

Rear number plate illumination and reversing lamp |
|
|
|
|
|
|
|
|
|
|
|
|
|
|
|
|
|
|
|
|
|
|
|
|
|
|
|
|
|
|
|
|
|
|
|
|
|
|
|
|
|
|
|
|
|
|
|
|
|
|
|
|
|
|
|
|
|
|
|
|
|
|
|
|
|
|
|
|
|
|
|
|
|
|
|
|
|
Clock
The illumination bulb can be replaced as follows:
1. Slacken screw beneath clock at underside of facia rail and withdraw clock.
2. Withdraw the bulb holder from the rear of the clock body.
3. Renew the bulb.
4. Replace the clock by reversing the sequence of removal operations.
Replacement bulb, clock illumination: Lucas No, 281, 12 v., 2 w. peanut.
Interior lights
The front interior light is switched on automatically when either door is opened and extinguished when the door is closed.
Each rear interior light is automatically switched on when the appropriate door is opened and extinguished when the door is closed.
They can be controlled manually as follows:
Front light, by means of small switch behind the facia rail.
Rear lights, by means of switches on the centre door pillars.
To replace a bulb:
Front lights
The bulb is visible behind the facia rail for direct replacement.
Rear lights
To gain access to the bulb, pull off the lamp front.
Replacement bulbs, interior lights: Lucas No. 254, 12 v., 6 w., Festoon. |
|
|
|
|
|
|
|
|
|
|
|
|
|
|
|
|
|
|
|
|

Front light bulb replacement |
|
|

Rear light bulb replacement. |
|
|
|
|
|
|

Clock bulb replacement
|
|
|
|
|
|
|
|
|
|
|
|
|
|
|
|
|
|
|
|
|
|
|
|
|
|
|
|
|
|
|
|
|
|
|
|
|
|
|
|
|
|
|
|
|
|
|
|
|
|
|
|
|
|
|
|
|
|
|
|
|
|
|
|
|
|
|
|
|
|
|
|
|
|
|
|
|
|
|
|
|
|
|
|
|
Instrument panel and warning light bulbs
Access to the instrument panel illumination bulbs is gained by swinging the instrument panel downwards. This is effected by removing the two screws from the top of the panel. The bulbs can then be renewed as necessary.
The warning light bulbs can be renewed after unscrewing the respective bezels from the front of the instrument panel.
Replacement bulbs:
Warning light bulbs, Lucas No. 987, 12 v., 2.2 MES.
Panel light bulbs, Lucas 987. 12 V., 2.2 w. MES.
|
|
|
|
|
|
|
|
|
|
|
|
|

Panel and warning light bulb replacement |
|
|
|
|
|
|
|
|
|
|
|
|
|
|
|
|
|
|
|
|
|
|
|
|
|
|
|
|
|
|
|
|
|
|
|
|
|
|
|
|
|
|
|
|
|
|
|
|
|
|
|
|
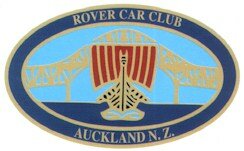 |
|
|
|
|
|
|
|
|
|
|
|
|
|
|
|
|
|
|
|
|
|
|
|
|
|
|
|
|
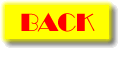 |
|
|
|
|
|
|
|
|
|
|
|
|
|
|
|
|
|
|
|
|
|
|
|
|
|
|
|
|
|
|
|
|
|
|
|
|
|
|
|
|
|
|
|
|
|
|
|
|
|
|
|
|
|
|
|
|
|
|
|
|
|
|
|
|
|
|
|
|
|