|
|
|
|
|
|
|
|
|
|
|
|
|
|
|
|
|
|
|
|
|
|
|
|
|
|
|
|
|
|
|
|
|
|
|
|
|
|
|
|
|
|
|
|
|
|
|
|
|
|
|
|
|
|
|
|
|
|
|
|
|
|
|
|
|
|
|
|
|
|
|
|
|
|
|
|
|
|
|
|
|
|
|
|
|
|
|
|
|
|
|
|
|
|
|
|
|
|
|
|
|
|
|
|
|
|
|
|
|
|
|
|
|
|
|
ELECTRICAL EQUIPMENT
BATTERY
The positive earth 12-volt battery is carried under the rear seat on the right-hand side and is accessible, after withdrawing the seat cushion, by removing the cover plate exposed.
At regular intervals check the battery level as follows
1. Wipe all dirt and moisture from the battery top.
2. Remove the filler plug from each cell in turn. If necessary add sufficient distilled water to raise the level to the top of the separators. Replace the filler plug. Avoid the use of a naked light when examining the cells.
Occasionally check the condition of the battery by measuring the specific gravity of the electrolyte in each cell, using a hydrometer. Specific gravity readings and their indications are as follows:
1.280 to 1.300 (32 degrees to 34 degrees Baumé) Battery fully charged.
About 1.210 (25 degrees Baumé) Battery about half discharged.
Below 1.150 (19 degrees Baumé) Battery fully discharged.
These figures assume an electrolyte temperate of 60 degrees F. (15.5 degrees C.). If one cell gives a reading very different from the rest, it may be that acid has leaked from the particular cell or there may be a short circuit between the plates0 in which case the battery should be inspected at a service depot.
Never leave the battery in a discharged condition for any length of time; it should be given a short refreshing charge every fortnight, to prevent permanent sulphation of the plates.
If the battery lugs have been removed for any reason they must always be refitted as follows
1. Clean terminal post and inside of the battery lug.
2. Fit plug to terminal post and lightly tap on to the taper of the post.
3. Smear vaseline or anti-corrosion grease in the hole for the retaining screw.
4. Replace screw, taking care not to over-tighten. On no account must the screw be used for pulling down the lug.
VOLTAGE CONTROL BOX
The voltage control, fuse and junction boxes are housed on the engine side of the scuttle, all but the control box being covered by a plate bearing an explanation of the connections; this plate is retained by two thumb screws and shakeproof washers.
The cut-out and regulator in the control box are set on initial assembly and must not be tampered with; the protecting cover is therefore sealed.
|
|
|
|
|
|
|
|
 |
|
|
|
|
|
|
|
|
|
|
|
|
|
|
|
|
|
|
|
|
|
|
|
|
|
|
|
|
|
|
|
|
|
|
|
|
|
|
|
Fig. 46. Voltage control box and fuse box.
A-Fuse “A2”.
B-Fuse “A4”.
C-Spare fuses. |
|
|
|
|
|
|
|
|
|
|
|
|
|
|
|
|
|
|
|
|
|
|
|
|
|
|
|
|
|
|
|
|
|
|
|
|
|
|
|
|
|
|
|
|
|
|
|
|
|
|
|
|
|
|
|
|
|
|
|
|
|
|
|
|
|
|
|
|
|
|
|
|
|
|
|
|
|
|
|
|
|
|
|
|
|
|
|
|
|
FUSES, BASIC
The fuse termed “A2” protects the accessories which are connected so that they operate irrespective of whether the ignition is on or off:
Clock, map light and interior lights.
The fuse termed “A4” protects the accessories which are connected so that they operate only when the ignition is switched on:
Windscreen wipers, heater, direction indicators, instrument panel lights, stop lights, petrol level gauge, petrol reserve switch and reverse light.
All other components are not fused.
A blown fuse is indicated by the failure of all the units protected by it and is confirmed by examination of the fuse. Before replacing a blown fuse, locate and remedy the fault in the wiring of the units which have failed. If the cause of the trouble cannot be found and a new fuse blows immediately, the car should be examined at a service depot.
Spare fuses are provided on the fuse box; only 35 amp. cartridge type fuses must be used.
|
|
|
|
|
|
|
|
|
|
|
|
|
|
|
|
|
|
|
|
|
|
|
 |
|
|
|
|
|
|
|
|
|
|
|
|
|
|
|
|
|
|
|
|
|
|
Fig. 47. Overdrive fuse unit.
A-Fuse.
B-Spare fuse. |
|
|
|
|
|
|
|
|
|
|
|
|
|
|
|
|
|
|
|
|
|
|
|
|
|
|
|
|
|
|
|
|
|
|
|
|
|
|
|
|
|
|
|
|
|
|
|
|
|
|
|
|
|
|
|
|
|
|
|
|
|
|
|
|
|
|
|
|
|
|
|
|
|
|
|
|
|
|
|
|
|
|
|
|
|
|
|
|
|
|
|
|
|
|
|
|
|
|
|
FUSES-WITH OVERDRIVE
The fuse unit for the overdrive electrical system is situated t& the right on the engine side of the scuttle.
A blown fuse is indicated as follows:
(a) When in normal, unable to engage overdrive.
(b) When in overdrive, the unit will re-engage normal drive irrespective of throttle opening.
Spare fuses are provided in the fuse box; only 35 amp cartridge type fuses must be used.
STARTER
In the event of the starter pinion becoming jammed in mesh with the flywheel, it can tisually be freed by withdrawing the dust cap and turning the starter armature by means of a spanner applied to the shaft extension at the commutator end.
DISTRIBUTOR
DISTRIBUTOR MAINTENANCE
At regular intervals, remove the distributor cap and lubricate as follows
1. Lightly smear the cam with clean engine oil,
2. Lift off the rotor and add a few drops of thin machine oil to lubricate the cam bearing and distributor shaft; push the rotor on the shaft as far as possible.
3. Place a drop of clean engine oil breaker lever pivot, taking care contacts. on the contact not to oil the contacts.
|
|
|
|
|
|
|
|
|
|
|
|
|
|
|
|
|
|
|
|
|
|
|
|
|
|
|
|
Fig. 48. Distributor (“75” and “90”)
A-Condenser.
B-Octane selector.
C-Cam.
D-Contact breaker pivot.
E-Vacuum unit.
F-Contact points.
G-Screws securing movable contact.
H-Cable securing nuts.
J-Carbon brush. |
|
|
|
|
|
|
|
|
|
|
|
 |
|
|
|
|
|
|
|
|
|
|
|
|
|
|
|
|
|
|
|
|
|
|
|
|
|
|
|
|
|
|
|
|
|
|
|
|
|
|
|
|
|
|
|
|
|
|
|
|
|
|
|
|
|
|
|
|
|
|
|
|
|
|
|
|
|
|
|
|
|
|
|
|
|
|
|
|
|
|
|
|
|
|
Periodically, clean the distributor as follows
1. Wipe the inside and outside of the cap with a soft, dry cloth; ensure that the small carbon brush works freely in its holder.
2. Slacken the nuts on the terminal block and lift off the spring and moving contact. Ensure that the contacts are free from grease or oil; if they are burned or blackened, clean with a fine carborundum stone or very fine emery cloth and wipe with a petrol-moistened cloth. Replace the moving contact.
3. Check and adjust the contact breaker clearance as follows:
(i) Remove the distributor cap and turn over the engine by hand until the contacts are fully open.
Periodically (see Page 18) the dynamo must be lubricated at the commutator end bearing by inserting the nozzle of a pump type oil can in the small central hole and injecting just sufficient engine oil to moisten the lubricating pad.
(ii) The clearance should be .014 to .016 in. (0,35 to 0,40 mm.) i.e., a .015 (0,38 mm.) feeler gauge should be a sliding fit between the contacts.
(iii) If necessary, slacken the two screws which secure the adjustable contact and turn the cam adjuster screw until the clearance is correct; re-tighten the screws.
(iv) Replace the distributor cap.
HIGH TENSION CABLES
7 mm, rubber-covered ignition cable must be used for replacement purposes when the original cable is cracked or perished. Connections are made as follows
Pass the moulded nut over the cable, bare the end of the cable, thread the wire through the washer from the original cable and bend back the wire strands.
DYNAMO
Periodically the dynamo must be lubricated at the ciommutator end bearing by inserting the nozzle of a pump type oil can in the small central hole and injecting sufficient engine oil to moisten the lubricating pad.
|
|
|
|
|
|
|
|
|
|
|
|
|
|
|
|
|
|
|
|
|
|
|
|
|
|
|
 |
|
|
|
|
|
|
|
|
|
|
|
|
Fig. 49, Dynamo lubrication.
A-Oil hole. |
|
|
|
|
|
|
|
|
|
|
|
|
|
|
|
|
|
|
|
|
|
|
|
|
|
|
|
|
|
|
|
|
|
|
|
|
|
|
|
|
|
|
|
|
|
|
|
|
|
|
|
|
|
|
|
|
|
|
|
|
|
|
|
|
|
|
|
|
|
|
|
|
|
|
|
|
|
|
|
|
|
|
|
HORNS
The twin bumper-mounted horns are adjusted on initial assembly and should not require attention for a considerable time. Adjustment merely takes up wear of moving parts and does not alter the pitch of the note; proceed as follows
1. Ascertain that the horn failure or faulty note is not due to some outside source, such as a discharged battery, loose connection, loose part adjacent to the horn, etc.
2. Disconnect the supply lead from the satisfactory horn, taking care that the end does not contact any part of the car. |
|
|
|
|
|
|
|
|
|
 |
|
|
|
|
|
|
|
|
|
|
|
|
|
|
|
|
|
|
|
|
|
|
|
|
|
|
|
|
|
|
|
|
|
|
|
|
|
|
Fig. 50. Horn adjustment.
A-Adjustable contact.
B-Locknut.
|
|
|
|
|
|
|
|
|
|
|
|
|
|
|
|
|
|
|
|
|
|
|
|
|
|
|
|
|
|
|
|
|
|
|
|
|
|
|
|
|
|
|
|
|
|
|
|
|
|
|
|
|
|
|
|
|
|
|
|
|
|
|
|
|
|
|
|
|
|
|
|
|
|
|
|
|
|
|
|
|
|
|
|
|
|
|
|
|
|
|
3. Remove the cover from the faulty horn. Slacken the locknut on the fixed contact and rotate the adjusting nut until the contacts are just separated (indicated by the horn failing to sound, when the horn ring is momentarily depressed).
4. Turn the nut half a revolution in the opposite direction and tighten the locknut.
5. Replace the cover and connect the other horn.
6. If the note is still unsatisfactory, the horn should be examined at a service depot. |
|
|
|
|
|
|
|
|
|
|
|
|
|
|
|
|
|
 |
|
|
|
|
|
|
|
|
|
|
|
|
|
|
|
Fig. 51. Headlamp bulb removal. |
|
|
|
|
|
|
|
|
|
|
|
|
|
|
|
|
|
|
|
|
|
|
|
|
|
|
|
|
|
|
|
|
|
|
|
|
|
|
|
|
|
|
|
|
|
|
|
|
|
|
|
|
|
|
|
|
|
|
|
|
|
|
|
|
|
|
|
|
|
|
|
|
|
|
|
|
|
|
|
|
|
|
|
|
HEADLAMPS
BULB REPLACEMENT
Slacken the screw at the bottom of the headlamp rim and lift off the rim and dust-excluding rubber. Press in the light unit against the tension of the springs on the three adjustment screws, turn it anti-clockwise and withdraw. Twist the adaptor in an anti-clockwise direction and pull it off the light unit; the bulb can then be replaced and the unit reassembled.
HEADLAMP SETTING
The headlamps should be set so that, when the car is normally loaded, the main driving beams are parallel with the road surface and with each other. If adjustment is required, remove the rim as described above. The vertical setting can then be made by turning the screw at the top of the lamp and horizontal adjustment by means of the screws at the side of the unit.
|
|
|
|
|
|
|
|
|
|
|
|
|
|
|
|
|
|
|
|
|
|
|
|
|
|
Fig. 52. Headlamps and fog lamp beam-setting board.
A-Board R.H.D. cars.
B-Board L.H.D. cars.
C-Concentrated area of light, L.H. headlamp.
D-Concentrated area of light, R.H. headlamp.
E-Concentrated area of light, Fog lamp (R.H.D. cars).
F-Concentrated area of light, Fog lamp when fitted to L.H.D. cars.
G-35.5 in. (890 mm.)
H-32.5 in. (812 mm.)
J-17 in. (430 mm.)
K-Ground level.
L-30.56 in. (1126 mm.) |
|
|
 |
|
|
|
|
|
|
|
|
|
|
|
|
|
|
|
|
|
|
|
|
|
|
|
|
|
|
|
|
|
|
|
|
|
|
|
|
|
|
|
|
|
|
|
|
|
|
|
|
|
|
|
|
|
|
|
|
|
|
|
|
|
|
|
|
|
|
|
|
|
|
|
|
|
|
|
|
FOG LAMP BULB REPLACEMENT
To fit a replacement bulb, unscrew the single securing screw at the bottom of the lamp rim and remove the rim and light unit assembly. The bulb can be removed from the back of the light unit when the spring clips attached to the bulb are pressed inwards.
Fix the spring clip to the replacement bulb and place the bulb in the holder, taking care that the marking “TOP” is uppermost. Reassemble the unit.
SIDE LAMP BULB REPLACEMENT, 1954-55 ONWARD
Remove the screw at the back of the lamp and detach the front of the lamp. The bulb can then be replaced and the unit reassembled.
|
|
|
|
|
|
|
|
|
|
|
|
|
|
|
|
|
|
|
|
|
|
|
|
|
|
|
|
 |
|
|
|
|
|
|
|
|
Fig. 53. Side lamp bulb removal, 1954-55 |
|
|
|
|
|
|
|
|
|
|
|
|
|
|
|
|
|
|
|
|
|
|
|
|
|
|
|
|
|
|
|
|
|
|
|
|
|
|
|
|
|
|
|
|
|
|
|
|
|
|
|
|
|
|
|
|
|
|
|
|
|
|
|
|
|
|
|
|
|
|
|
|
|
|
|
|
|
SIDE LAMP BULB REPLACEMENT, 1956
Prise up rubber lip and remove chrome rim complete with glass. The bulb can then be replaced and the unit reassembled. |
|
|
|
|
|
|
 |
|
|
|
|
|
|
|
|
|
|
|
|
|
|
|
|
|
|
|
|
|
|
|
|
|
|
|
|
|
|
|
|
|
|
|
|
Fig. 54. Side lamp bulb removal, 1956 onward |
|
|
|
|
|
|
|
|
|
|
|
|
|
|
|
|
|
|
|
|
|
|
|
|
|
|
|
|
|
|
|
|
|
|
|
|
|
|
|
|
|
|
|
|
|
|
|
|
|
|
|
|
|
|
|
|
|
|
|
|
|
|
|
|
|
|
|
|
|
|
|
|
|
|
|
|
|
|
|
|
|
|
|
|
STOP/TAIL LAMP BULB REPLACEMENT, 1954 Models
Slacken the two securing screws and remove the rim assembly. The outer (dual filament) bulb is the stop/tail bulb; on North American cars a second bulb is fitted in the inner socket to act as a direction indicator. |
|
|
|
|
|
|
|
|
|
|
|
|
|
|
|
|
|
 |
|
|
|
|
|
|
|
|
|
|
|
|
|
|
|
|
|
Fig. 55. Stop/tail lamp bulb removal |
|
|
|
|
|
|
|
|
|
|
|
|
|
|
|
|
|
|
|
|
|
|
|
|
|
|
|
|
|
|
|
|
|
|
|
|
|
|
|
|
|
|
|
|
|
|
|
|
|
|
|
|
|
|
|
|
|
|
|
|
|
|
|
|
|
|
|
|
|
|
|
|
|
|
|
|
|
|
|
|
|
|
|
|
|
|
|
|
|
|
|
|
|
|
|
|
REAR LAMP BULB REPLACEMENT, 1955 ONWARD
Slacken the two securing screws and remove the rim assembly. The lower (dual filament) bulb is the stop, tail bulb while the second bulb, fitted in the upper socket, acts as a direction indicator. |
|
|
 |
|
|
|
|
|
|
|
|
|
|
|
|
|
|
|
|
|
|
|
|
|
|
|
|
|
|
|
|
|
|
|
|
|
|
|
|
|
|
Fig. 56. Stop/tail lamp bulb removal. |
|
|
|
|
|
|
|
|
|
|
|
|
|
|
|
|
|
|
|
|
|
|
|
|
|
|
|
|
|
|
|
|
|
|
|
|
|
|
|
|
|
|
|
|
|
REAR NUMBER PLATE AND REVERSE LAMP BULB REPLACEMENT
Slacken the two securing screws and remove the rim assembly. The reverse lamp bulb is the centre one; the outer bulbs provide number plate illumination |
|
|
|
|
|
|
|
|
|
|
|
|
|
|
|
|
|
|
|
|
|
 |
|
|
|
|
|
|
|
|
|
|
|
|
|
Fig. 57. Rear number plate and reverse lamp bulb removal. |
|
|
|
|
|
|
|
|
|
|
|
|
|
|
|
|
|
|
|
|
|
|
|
|
|
|
|
|
|
|
|
|
|
|
|
|
|
|
|
|
|
|
|
|
|
|
|
|
|
|
|
|
|
|
|
|
|
|
|
|
|
|
|
|
|
|
|
|
|
|
|
|
|
|
|
|
|
|
|
|
|
|
|
|
|
TRAFFICATORS, 1954 models
TRAFFICATOR LUBRICATION
Every 6,000 miles (10.000 Km.) lubricate the trafficators as follows
1. Apply one drop of thin machine oil (by brush) to the catch pin between the arm and the operating mechanism.
2. Remove the arm fixing screw, slide off the arm cover and apply a drop of thin machine oil to the pivot pin. Replace the cover, making sure that the side plates engage with the slots on the underside of the spindle bearing.
TRAFFICATOR BULB REPLACEMENT
Remove the arm fixing screw and slide off the arm cover, Renew the bulb and replace the cover, making sure that the side plates engage with the slots on the underside of the spindle bearing.
|
|
|
|
|
|
|
|
|
 |
|
|
|
|
|
|
|
|
|
|
|
|
|
|
|
|
|
|
|
|
|
|
|
|
|
|
|
|
|
|
|
|
|
|
|
|
|
|
|
|
|
|
|
|
Fig. 58. Trafficator maintenance.
A-Catch pin.
B-Pivot pin.
C-Arm Cover.
D-Bulb. |
|
|
|
|
|
|
|
|
|
|
|
|
|
|
|
|
|
|
|
|
|
|
|
|
|
|
|
|
|
|
|
|
|
|
|
|
|
|
|
|
|
|
|
|
|
|
|
|
|
|
|
|
|
|
|
|
|
|
|
|
|
|
|
|
|
|
|
|
|
|
|
|
|
|
|
|
|
|
|
|
|
|
|
|
|
|
|
|
|
|
|
|
|
|
|
|
|
|
DIRECTION INDICATOR LAMP BULB REPLACEMENT, 1955 ONWARD
Turn the lamp glass and rim in an anti-dockwise direction until it can be lifted off; renew the bulb, press on the glass and rim and turn as far as possible. |
|
|
|
|
 |
|
|
Fig. 59. Front indicator lamp bulb removal. |
|
|
|
|
|
|
|
|
|
|
|
|
|
|
|
|
|
|
|
|
|
|
|
|
|
|
|
|
|
|
|
|
|
|
|
|
|
|
|
|
|
|
|
|
|
|
|
|
|
|
|
|
|
|
|
|
|
|
|
|
|
|
|
|
|
|
|
|
|
|
|
|
|
|
|
|
|
|
|
|
|
|
|
|
|
|
|
|
|
|
|
|
|
|
|
|
|
|
|
|
REPLACEMENT BULBS. |
|
|
|
|
|
|
|
|
|
|
|
|
|
|
|
|
|
|
|
|
|
|
|
|
|
|
|
|
|
|
|
|
|
|
|
|
|
|
|
|
|
|
|
|
|
|
|
|
|
|
|
|
|
|
|
|
|
|
|
|
|
|
|
|
|
|
|
|
|
|
|
|
|
 |
|
|
|
|
|
|
|
|
|
|
|
|
|
|
|
|
|
|
LUGGAGE BOOT LAMP BULB REPLACEMENT
The bulb is visible in the boot lid for direct replacement.
INSTRUMENT PANEL AND WARNING LIGHT BULB REPLACEMENT
Should a warning light bulb burn out, operation of the corresponding component will not be affected, but it should be replaced at the earliest opportunity to safeguard that particular item of equipment. The ignition, mixture control and oil pressure warning light bulbs can be renewed after unscrewing the respective bezels from the front of the instrument panel.
Access to the instrument panel illumination and headlamp warning light bulbs is gained by swinging down the instrument panel facia; this is effected by releasing the speedometer cable from the clip on the engine and removing the two screws at the top of the panel (Fig. 3).
CLOCK
ILLUMINATION BULB REPLACEMENT
1. Slacken screw beneath clock at underside of facia rail and withdraw clock.
2. Withdraw the rubber cover and bulb holder from the rear of the clock body.
3. Renew the bulb.
4. Replace the clock by reversing the sequence of removal operations.
|
|
|
|
|
|
|
|
|
|
|
|
|
|
|
|
|
|
|
|
|
|
|
|
|
|
|
|
|
|
|
|
|
|
|
|
|
|
|
|
|
|
|
|
|
|
|
|
|
|
|
|
|
|
|
|
|
|
|
|
|
|
|
|
|
|
|
 |
|
|
|
|
|
|
|
|
|
Fig. 60. Clock, 1959 models illustrated. |
|
|
|
|
|
|
|
|
|
|
|
|
|
|
|
|
|
|
|
|
|
|
|
|
|
|
|
|
|
|
|
|
|
|
|
|
CLOCK ADJUSTMENT, 1954-58 models
To adjust the hands of the electric clock, push in the knob on the left of the instrument (just behind the facia rail) and turn in the required direction.
CLOCK ADJUSTMENT, 1959 models
1. Adjust as necessary by means of the regulating screw in the left-hand front face of the clock.
INTERIOR LAMP BULB REPLACEMENT
To gain access to the bulb, pull off the lamp front.
MAP LIGHT BULB REPLACEMENT.
The bulb is visible behind the facia rail for direct replacement.
WINDSCREEN WIPERS
WINDSCREEN WIPER BLADE REPLACEMENT
Hold the wiper arm away from the windscreen ~nd withdraw the slotted spring fastening of the blade from the curved wrist of the arm.
Fit the new blade by reversing this sequence of operations.
BODYWORK
DOORS
The door panels on the Rover “60” “75” “90” and “105” are made from aluminium for lightness and protection against corrosion. This gives many advantages, but the panels can be more easily dented than those made of steel.
It is important therefore that doors with aluminium panels are closed by using the exterior handles only, and not by pushing against the panel.
CLEANING BODY
It is always preferable to clean the bodywork with water and sponge, using plenty of water; wherever possible the surface should be freely hosed. After drying with a chamois leather, it should be polished in the usual manner, using any of the good brands of wax car polish.
As an alternative, if the body is only dusty, it can be wiped over the a soft, dry cloth and then polished, but great care must be taken to avoid scratching the surface.
It is well periodically to wash the underside of the car, to prevent mud pockets and the consequent tendency for rust formation.
BODY TOUCH-UP PAINT
The body touch-up pencil supplied is loaded with 8 c.c. of cellulose base paint. It is suitable for touching up small scratches, etc., and should be used as follows
1. Thoroughly clean surface to be painted.
2. Shake the container well.
3. Remove cap, tip down and apply.
4. Regulate flow by pressure on brush.
5. Wipe nozzle, container and cap after use and replace cap tightly.
NOTE: With dual colour cars the pencil supplied is suitable for the lower colour only.
CLEANING CHROMIUM PLATING
Chromium plating cannot rust, but in instances where it is used on ferrous metals, it does not prevent the accumulation of red oxide on the chromium surface.
Although continual polishing is not necessary, dirt and tar must be removed periodically if the original high polish is to be maintained. Ordinary metal polishes cannot be used, as some of them contain solutions which act as a solvent to chromium.
To clean off mud and dirt, wash with water and dry with a leather.
To remove oxide or tar, use any good brand of polish that has been specially prepared for chromium plate.
|
|
|
|
|
|
|
|
|
|
|
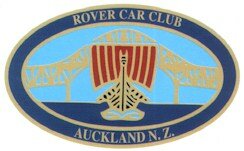 |
|
|
|
|
|
|
|
|
|
|
|
|
|
|
|
|
|
|
|
|
|
|
|
|
|
|
|
|
|
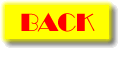 |
|
|
|
|
|
|
|
|
|
|
|
|
|
|
|
|
|
|
|
|
|
|
|
|
|
|
|
|
|
|
|
|
|
|
|