|
|
|
|
|
|
|
|
|
|
|
|
|
|
|
|
|
|
|
|
|
|
|
|
|
|
|
|
|
|
|
|
|
|
|
|
|
|
|
|
|
|
|
|
|
|
|
|
|
|
|
|
|
|
|
|
|
|
|
|
|
|
|
|
|
|
|
|
|
|
|
BRAKE SYSTEM
BRAKE FLUID RESERVOIR
The fluid reservoir for the hydraulic brake system is mounted on the engine side of the scuttle on the same side as the brake pedal.
The correct fluid level is with the reservoir three-quarters full; occasionally, remove the filler cap and replenish as necessary, using only Girling Crimson
Brake Fluid (obtainable from any Rover distributor or dealer).
It is advisable to check this point regularly, as shortage of fluid will result in gradual deterioration of the brakes which may not be noticed by the driver.
BRAKE SYSTEM. '90" (1956 onwards) and "105" MODELS
Servo-assisted brakes are fitted to all "90" (1956 onwards) and "105" models. Briefly this consists of a hydraulic system similar to the "60' and "75" models, with the addition of a slave master cylinder, operated by a servo vacuum unit which is connected to the induction system via a reservoir tank.
As the power for this braking system is derived from the engine itself, it is inadvisable to coast downhill with the engine stopped.
Should the servo unit fail the brakes will continue to function through the normal hydraulic system when the brake pedal is depressed, but more foot pressure will be required than formerly.
The servo vacuum reservoir tank will allow servo assistance for a maximum of two applications after the engine has stopped.
FOOT BRAKE ADJUSTMENT
When brake lining wear has reached a point where the pedal travel becomes excessive, it is necessary to adjust the shoes in closer relation to the drum. Proceed as follows
FRONT BRAKES, "60", "75" and 1954-55 "90"
Jack up each front wheel in turn. On the back face of the brake anchor plate (at 6 o'clock and 12 o'clock) are two adjustment bolts (A) giving independent adjustment for each brake shoe.
Slacken both adjusters as far as possible in an anti-clockwise direction (looking at the rear of the anchor plate) to give maximum clearance for the shoes.
|
|
|
|
|
|
|
|
 |
|
|
|
|
|
|
|
|
|
|
|
|
|
|
|
|
|
|
|
|
|
|
|
|
|
Fig. 29. Front brake adjustment-"60", "75" and 1954-55 '90"
A-Adjustment points.
B-Bleed nipple.
C-Shoe steady post.
|
|
|
|
|
|
|
|
|
|
|
|
|
|
|
|
|
|
|
|
|
|
|
|
|
|
|
|
|
|
Rotate one adjuster clockwise until that brake shoe contacts the drum, then turn it back one or two serrations until the road wheel just rotates freely. Set the second adjuster in a similar manner.
Re peat these operations for the other front wheel.
FRONT BRAKES "90" (1956 onwards) and "105"
Hydro-static hydraulic two trailing shoe brakes are fitted on the front of the "90" (1956 onwards) and "105" and the correct brake shoe adjustment is automatically maintained, no provision is therefore made for adjustment.
REAR BRAKES
Release the hand brake. Adjustment is made by the spindle (A) at 2 o'clock on the left-hand brake unit (looking at the rear face of the anchor plate) and at 10 o'clock on the right-hand unit; during rotation of the adjuster, a "click" will be felt and heard at each quarter revolution.
Rotate the spindle as far as possible in a clockwise direction, i.e., until the brake shoes contact the drum. Then unscrew the adjuster two clicks, when the wheel should be quite free to rotate. Repeat for the other wheel.
|
|
|
|
|
|
|
|
|
|
|
|
|
|
|
|
|
|
|
 |
|
|
|
|
|
|
|
|
|
Fig. 30. Rear brake adjustment.
A-Adjustment point.
B-Bleed nipple.
C-Shoe steady post.
|
|
|
|
|
|
|
|
|
|
|
|
|
|
|
|
|
|
|
|
|
|
|
|
|
|
|
|
|
|
|
|
|
|
|
|
|
|
|
|
|
|
|
|
|
|
|
|
|
|
|
|
|
|
|
|
|
|
LINKAGE ADJUSTMENT
No attempt must be made to adjust the rods or levers of the brake linkage; they are correctly set on initial assembly and no further attention is necessary.
HAND BRAKE ADJUSTMENT.
If movement on the lever should become excessive, it may be reduced by means of the adjustment on the operating rod, accessible when the cover is removed.
The linkage should be set so that the lever has one or two "clicks" free movement in the "off" position.
|
|
|
|
|
|
|
|
|
|
|
|
|
|
|
|
|
|
|
|
 |
|
|
|
|
 |
|
|
|
|
|
|
|
|
|
|
|
|
|
|
|
|
|
|
|
|
|
|
|
|
|
Fig.31. Hand brake adjustment, 1954 models.
A-Adjuster nut.
B-Locknut. |
|
|
|
|
|
|
|
|
|
|
|
|
|
|
|
|
|
|
Fig. 32. Hand brake adjustment, 1955-59 models.
A-Adjusting nut. B-Locknut |
|
|
|
|
|
|
|
|
|
|
|
|
|
|
|
|
|
|
|
|
|
|
|
|
|
|
|
|
|
|
|
|
|
|
|
|
|
|
|
|
|
|
|
|
|
|
|
|
BLEEDING THE BRAKE SYSTEM
If the level of fluid in the reservoir is allowed to fall too low, or if any section of the brake pipe system is disconnected, the brakes will feel "spongy", due to air having been absorbed into the system. This air lock must be removed by bleeding the hydraulic system at the wheel cylinders; bleeding must always be carried out at all wheels, irrespective of which portion of the pipe-line is affected:
1. Slacken the shoe adjustment bolts right off.
2. Attach a length of rubber tubing to the bleed nipple on the wheel unit farthest from the brake pedal and place the lower end of the tube in a glass jar.
3. Slacken the bleed s4ew behind the nipple and pump the brake pedal sharply two or three times and then more slowly, pausing at each end of the stroke, until the fluid issuing from the tube shows no signs of air bubbles when the tube is held below the surface of the fluid in the jar. Keep the foot pedal depressed.
4. Hold the tube under the fluid surface and tighten the bleed screw.
5. Repeat for the other three wheels in turn, finishing at the one nearest the brake pedal.
6. Readjust the brakes.
The fluid in the reservoir should be replenished throughout the operation, to prevent another air-lock being formed.
FUEL SYSTEM
The fuel system comprises the tank, pipe-lines, pump, sediment howl, carburetter and air cleaner; the petrol feed pipe from the tank under the luggage boot floor runs to the pump in the right-hand rear corner of the boot and thence along the right-hand chassis side member to the carburetter.
It is most important that the entire system be kept clean and free from leaks.
DRAINING THE FUEL SYSTEM
If the car is to be stored for an extended period, the fuel system should be completely drained to prevent the formation of gum in the pump and carburetters. Remove the drain plug from the bottom of the petrol tank and replace when the tank is empty; then run the engine until the petrol in the pipe-line is exhausted.
PETROL PUMP
The petrol pump, fitted in the luggage boot and protected by a quickly detachable cover, is wired through the ignition; it will operate immediately the ignition is switched on, so filling the carburetter float chamber and ensuring easy starting.
CLEANING PETROL PUMP FILTER
Should the pump filter become choked, it can be withdrawn, after removing the pump cover, by unscrewing the hexagon brass plug in the bottom of the pump body. Clean thoroughly in petrol, using a stiff brush; never use rag for cleaning this type of filter.
PETROL PUMP FAULT LOCATION
If petrol pump trouble is suspected:-
1. Disconnect the pump outlet pipe and switch on the ignition:
A. If the pump then operates satisfactorily, the trouble is due to either:-
(i) Blockage of the pipe to the sediment bowl.
(ii) Blockage of the sediment bowl which can be cured by cleaning. See below.
(iii) Blockage of the pipe from the sediment bowl to the carburetter.
Or (iv) Blockage of the carburetter(s),
B. If the pump still does not operate correctly, the trouble may be due to either:
(i) Blockage of the pipe to the tank, which can be cleared by blowing down it with a tyre pump.
(ii) Poor connection in the pump wiring. Disconnect the lead from the feed terminal (c) and strike it against a metallic part of the body; the appearance of sparks will indicate that the current supply is in order.
NOTE-Care should be taken during this test, as loose petrol or vapour may cause a fire.
Or (iii) Dirty pump contact points. Remove the cover (D) and touch the terminal (c) with the lead. If the pump does not operate when the points (E) are in contact and a spark cannot be struck off the terminal, then the points must be cleaned by sliding a piece of card between them.
Failure to locate and rectify the fault in this manner will indicate that the pump itself is at fault and the local Rover distributor or dealer should be consulted.
|
|
|
|
|
|
|
|
|
|
|
|
|
 |
|
|
|
|
|
|
|
|
|
|
|
Fig. 33. Petrol pump.
A-Gauze filter.
B-Filter plug.
C-Feed terminal.
D-Bakelite cover.
E-Contact points.
F-Inlet union.
G-Outlet union.
H-Valve cage.
J-Thick washer.
K-Thin washer.
|
|
|
|
|
|
|
|
|
|
|
|
|
|
|
|
|
|
|
|
|
|
|
|
|
|
|
|
|
|
|
|
|
|
|
|
|
|
|
|
|
|
|
|
|
|
|
|
|
|
|
|
|
|
|
|
|
If the pump becomes noisy in operation, allow it to deliver directly into a can; if the delivery pipe is submerged in the petrol and bubbles appear, an air leak on the suction side of the pump is indicated, which must be found and cured.
If the pump becomes hot in operation or keeps on beating without delivering petrol, a choked filter or dirt in the pump valves is indicated. To locate and remove the obstruction in the valve, unscrew the top union (G) from the pump and lift out the valve cage (H). When replacing the cage, ensure that the thin hard red fibre washer (K) is below the cage and the thick orange-coloured one (J) above.
SEDIMENT BOWL
The sediment bowl, mounted on the wing valance, provides an additional filter between the pump and carburetter,
Occasionally, remove the glass bowl by slackening the thumbscrew and swinging the wire holder aside. Remove the gauze filter from the body of the unit and wash it and the bowl in petrol. Replace the gauze correctly over the inlet nozzle, ensure that the sealing washer is in good condition, and replace the bowl.
AIR CLEANER AND SILENCER
Two types of air cleaner and silencer may be found on the various "60," "75", "90" and "105" models:
(a) Oil-wetted gauze
(b) (b) Oil bath.
ROUTINE MAINTENANCE
Attention to the air cleaner is extremely important, as engine wear generally will be seriously affected if the car is run withan excessive amount of dirt in the cleaner.
Oil-wetted gauze type. Under clean road conditions the air silencer and cleaner should be cleaned every 6,000 miles (10.000 Km.), but in cases where
the car is operated under extremely dusty conditions, attention must be more frequent. Proceed as follows:
1. Remove the nut, spring washer and bolt securing the air silencer to its support.
2. Slacken the hose clip securing the air silencer to the intake elbow and remove the air silencer complete.
3. Wash the gauze by swilling the unit in a dish of petrol.
4. Re-wet the gauze with clean engine oil and shake off the surplus.
5. Replace the air silencer.
|
|
|
|
|
|
|
|
|
|
|
|
|
|
|
|
|
|
|
 |
|
|
|
|
|
|
Fig. 34. Oil-wetted gauze type air cleaner. |
|
|
|
|
|
|
|
|
|
|
|
|
|
|
|
|
|
|
|
|
|
|
|
|
|
|
|
|
|
|
|
|
|
|
|
|
|
|
|
|
|
|
|
|
|
|
|
|
|
|
|
|
|
|
Oil bath type. Under clean road conditions, the oil bath should be cleaned every 3,000 miles (5.000 Km.), but in cases where the car is operated under extremely dusty conditions, attention must be more frequent. Proceed as follows
1. Slacken the hose clips securing the air cleaner top cover to the silencer duct; unscrew the knurled nut securing the top cover and remove the air cleaner complete.
2. Lift off the top cover and remove the filter element from the oil bath.
3. Unscrew the container from the stud on the support bracket and clean out all dirty oil and sludge. Replace container and refill with fresh engine oil to the indicated level; the capacity is approximately 1 pint (0,5 litre).
4. Rinse the filter element in paraffin and shake off the surplus.
5. Ensure that the sealing washers are in position and intact and reassemble the unit. |
|
|
|
|
|
|
|
|
 |
|
|
|
|
|
|
|
|
|
|
|
|
|
|
|
|
|
|
|
|
Fig. 35. Oil bath type air cleaner.
|
|
|
|
|
|
|
|
|
|
|
|
|
|
|
|
|
|
|
|
|
|
|
|
|
|
|
|
|
|
|
|
|
|
|
|
|
|
|
|
|
|
|
|
|
|
|
|
|
|
CARBURETTER-"60", "75" (1955 onwards), and "90" models.
The horizontal dust-proof carburetter is carefully adjusted on assembly and, apart from the few items of routine maintenance indicated, normally requires no further attention.
NOTE: Twin horizontal dust-proof carburetters are fitted to the 1954 "75" and to "105" models.
CARBURETTER MAINTENANCE
At regular intervals (see Page 18), remove the hydraulic damper(s) from the carburetter(s) by unscrewing the brass cap on top of the suction chamber; replenish the damper reservoir as necessary with S.A.E.20 oil and replace.
Occasionally disconnect the petrol pipe from the carburetter and withdraw the thimble filter(s) from the float chamber cover(s). Clean the filter in petrol, using a stiff brush.
CARBURETTER FAULT LOCATION
If engine trouble is traced to the carburetter(s) the more probable faults are
1. Sticking piston. To verify, remove the intake elbow and lift the piston by hand. If it does not rise evenly and fall back on to its seat when released, clean the suction chamber and piston in petrol and dry thoroughly; do not lubricate these parts. If still unsatisfactory, the piston damper
may not be working correctly.
2. Water or dirt in the carburetter(s). To remedy, remove the intake manifold, start the engine, open the throttle and block up the air intake(s) momentarily; close the throttle when the engine starts to race.
3. Float chamber flooding. This is caused by grit in the float needle valve and can be cured by cleaning.
4. Float needle sticking. A sticking float needle will result in lack of engine power, apparently through lack of petrol and can be confirmed by disconnecting the petrol feed pipe from the carburetter, when a satisfactory flow from the pump should be obtained. To remedy, clean the float chamber and needle valve.
|
|
|
|
 |
|
|
|
|
|
|
|
|
|
|
|
|
|
|
|
|
|
|
Fig. 36. Carburetter.
A-Oil filler cap.
B-Throttle stop screw.
C-Jet adjusting nut. |
|
|
|
|
|
|
|
|
|
|
|
|
|
|
|
|
|
|
|
|
|
|
|
|
|
|
|
|
|
|
|
|
|
|
|
|
|
|
|
|
|
|
|
|
|
|
|
|
|
|
CARBURETTER ADJUSTMENT, 1954 "75"
The only adjustments provided at each carburetter are the throttle stop screw to regulate the idling speed and the jet nut to obtain the correct mixture at that speed; if these two settings are correct, the mixture strength is automatically adjusted over the whole speed range.
Should synchronisation between the carburetters be lost for any reason, re-adjust as follows:
1. Remove the intake manifold.
2. Unscrew both throttle stop screws clear of the abutment flanges and slacken the throttle spindle connection. Close both throttles completely and re-tighten the connection. Run the engine up to normal operating temperature and adjust the throttle stop screws by equal amounts to give the correct idling speed.
3. Lift one carburetter piston slightly. If the engine then speeds up, the mixture is too strong and the jet nut must be screwed up; if the engine stops immediately, the mixture is too weak and the jet should be gradually unscrewed. If the engine just falters or continues to run unevenly, the adjustment for that carburetter is correct. Repeat for the other unit.
4. It may be necessary to slightly correct the settings when the intake manifold is replaced.
CARBURETTER ADJUSTMENT '60", "75" (1955 onward) and "90"
The only adjustments provided at the carburetter are the throttle stop screw to regulate the idling speed and the jet nut to obtain the correct mixture at that speed; if these two settings are correct, the mixture strength is automatically adjusted over the whole speed range.
Should the carburetter require tuning for any reason, proceed as follows:
1. Run the engine up to normal operating temperature and, if necessary, adjust the throttle stop screw to give the correct idling speed.
2. Lift the carburetter piston slightly by means of the lift pin situated on the right of the carburetterbody. If the engine then speeds up, the mixture is too strong and the jet must be screwed up; if the engine stops immediately, the mixture is too weak and the jet should be gradually unscrewed. If the engine just falters and continues to run unevenly, the adjustment is correct.
CARBURETTER ADJUSTMENT "105"
The carburetters fitted to the "105" differ from those on the "60", "75" and "90" in that, on the older type, the jet is controlled by a nut, and the engine speed is determined by adjustment of the throttle; on the new type the jet is controlled by a screw and the engine speed is determined by a "slow-run" valve. The mixture is adjusted on the jet adjusting screw, screw in to enrich, unscrew to weaken. When the mixture is correct the slow-running adjustment should be re-set with the slow-valve only.
|
|
|
|
|
|
|
|
|
|
|
|
|
|
|
|
|
|
|
|
|
|
|
|
|
|
|
|
|
|
|
|
|
|
|
|
|
|
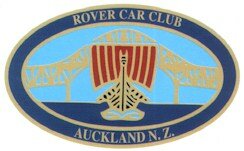 |
|
|
|
|
|
|
|
|
|
|
|
|
|
|
|
|
|
|
|
|
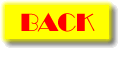 |
|
|
|
|
|
|
|
|
|
|
|
|
|
|
|
|
|
|
|
|
|
|
|
|
|
|
|
|
|
|
|
|
|
|
|
|
|
|
|
|
|
|
|
|
|
|
|
|
|
|
|